|
Cadena de Suministros Inteligente: Reposición de Materiales Automatizada
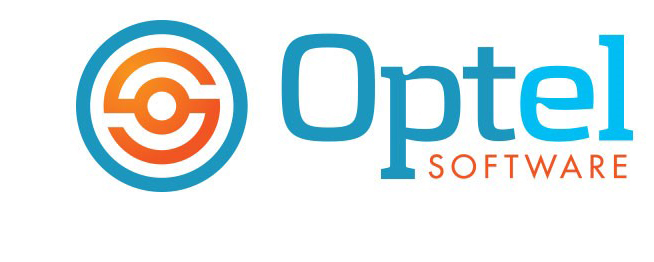
La meta final de Industry 4.0 es una fábrica de luces apagadas que puede correr desatendida por períodos de tiempo extendidos. Uno de los componentes de manufactura de luces apagadas es la reposición automatizada de suministro de materiales a la línea de ensamble. Sin embargo, esa no es una solución práctica en producción de alto volumen. El material está típicamente almacenado en un almacén de punto de uso o tomado de un almacén central cuando se necesita. La figura 1 describe un suministro automatizado de reposición de material de torres inteligentes de material, involucrando el siguiente equipo:
- Un sistema MES que monitorea el consume de material en tiempo real de las máquinas de levantar y colocar
- Torres de Material
- Vehículos Guiados Automatizados (AGVs, por su siglas en inglés)
- Robots
Figura 1. Equipo usado para reposición automatizada de material
El sistema MES monitorea el consumo de material y desperdicio en tiempo real, recolecta datos de rastreabilidad, alerta en casos de exceso de desperdicio y bloquea la máquina si se prefiere, calcula el OEE en tiempo real, identifica los cuellos de botella y tiempos de ciclo y, manda señales de reposición. Una señal de reposición es enviada cuando el tiempo que toma usar un carrete cae debajo del umbral del tiempo de reposición. La señal de reposición es enviada a la torre de material para proveer un nuevo carrete de ese número de parte. Ocasionalmente, una torre de material da servicio a más de una línea. En ese caso las líneas compiten por materiales, tomándolo de acuerdo a la regla FIFO. A cada línea se asigna una lista de torres de material de las cuales pueden requerir material, en un orden de prioridad. Si el material no se encuentra en ninguna de las torres asignadas, se genera una alerta.
Industry 4.0 asume islas independientes de automatización inteligente para hablar una a otra, así que, idealmente, el protocolo de comunicación para reposición automatizada de material sería como sigue:
- El sistema MES manda mensajes a la torre de material: “Revisar si tiene un carrete de un dado número de parte y si es así, mandarlo a la ubicación de la máquina.”
- Si la torre inteligente de material manda un mensaje de “carrete no encontrado” al sistema MES, manda un mensaje de regreso al sistema MES, luego va a través de la lista de materiales de las torres asignadas a esa línea hasta que encuentra un carrete de reposición pero si no se encuentra, se genera una alerta al personal de inventario
- La primera torre de material que encuentra un nuevo carrete del número de parte manda un mensaje al AGV: “Posiciónese usted para tomar el carrete a mano y llévelo a la ubicación de la máquina.”
- El robot dentro de la torre de material recoge el carrete requerido y manda un mensaje al robot asignado a la ubicación de donde lo va a recoger en la torre de material: “Posiciónese para recoger el carrete.”
- La torre de material coloca el carrete en la charola de donde lo va a tomar y manda un mensaje al robot: “El carrete está en la charola, recójalo.”
- El robot toma el carrete y manda un mensaje a la torre de material: “El carrete fue tomado de la charola.”
- Una vez posicionado en la ubicación de levantamiento de la torre de material, el AGV (vía su supervisor) manda un mensaje al robot: “Estoy en la posición de levantamiento, listo para tomar el carrete.”
- El robot coloca el carrete en el AGV y manda un mensaje al AGV: “Carrete dejado.”
- El AGV manda un mensaje de OK al robot y toma el carrete a la máquina de levantar y colocar.
En este punto, esta solución es muy difícil de implementar debido a una falta de un protocolo de comunicación M2M sin soporte por los vendedores de equipo. Un software de fábrica inteligente necesitaría persuadir a los vendedores de torres de material, robots y AGVs a implementar interfaces específicas, lo cual es una tarea retadora. Una solución intermedia es que el sistema MES controle toda la comunicación intermedia descrita y se comunique con las torres de material, AGVs y robots. Eso, sin embargo, no cumple con la idea de Industry 4.0 por las siguientes dos razones:
- Industry 4.0 asume islas independientes de automatización inteligente que se comunican unas con otras sin un sistema de control central. Las máquinas inteligentes son un componente importante de Indutry 4.0.
- El sistema MES será obsoleto en fábricas inteligentes que implementen completamente Industry 4.0. En nuestro diseño, el sistema MES debe ser reemplazado por máquinas inteligentes de levantar-y-colocar que monitorean el consumo de material y envía señales de reposición, entre otras tareas.
La asociación IPC anunció recientemente que ha aceptado el Protocolo Avanzado de Colas (AMQP por sus siglas en inglés) como el protocolo de transporte para comunicación de máquina a máquina como parte de la Iniciativa de Fábrica Conectada (CFX). Un grupo de vendedores está desarrollando el Estándar Hermes para comunicación de máquina a máquina independiente del vendedor en ensamble de SMT. Esperamos que la industria se decidirá pronto por uno de estos protocolos y los vendedores implementarán el apoyo para su equipo.
Aunque la solución propuesta satisfice completamente los requerimientos de reposición automatizada de material, las siguientes mejoras son necesarias para hacerlo exitoso en ambientes complejos de producción.
Las plantas grandes de ensamble electrónico, tales como la mostrada en la Figura 1 con 24 líneas de ensamble, pueden necesitar numerosas torres de materiales, robots y AGVs. El costo es alto, los Robots y AGVs solos pueden costar $30,000-50,000 cada uno. Ese precio bajará a medida que las aplicaciones de robots se expandan en ensamble electrónico. El costo puede ser justificado con reducción de mano de obra y un mayor rendimiento de la línea. No hay alternativa, sin embargo, con este enfoque si se debe implementar una verdadera fábrica de luces apagadas.
- El tráfico de AGV y la coordinación de la misión se convierten en un problema significativo en plantas grandes. Un control de coordinación descentralizado de AGVs necesita ser implementado [1].
- No hay un protocolo estándar para comunicación entre torres de material, robots y AGVs. El sistema MES usó un SOAP API patentado por el vendedor de la torre para comunicarse a la torre. Para que la torre controle el robot y los AGVs, el vendedor de la torre debe implementar diferentes interfaces para marcas diferentes de robots y AGVs. Un estándar de comunicación M2M es la solución pero, todavía no tenemos tal estándar implementado entre los vendedores de equipo.
- No es práctico asumir que los AGVs tomarán un carrete a tiempo y lo entregarán a la máquina. El control de coordinación del AGV debe permitir recoger carretes de múltiples torres de material y llevarlos a la línea en una misión del AGV.
El umbral de tiempo de reposición para emitir señales de reposición debe ser calculado dinámicamente basado en el tiempo de transporte y recolección de un grupo de carretes que deben ejecutarse pronto, en vez de un tiempo de reposición fijado por la máquina o la línea.
Archives:
|